Local woodworker carries on traditional logging practices
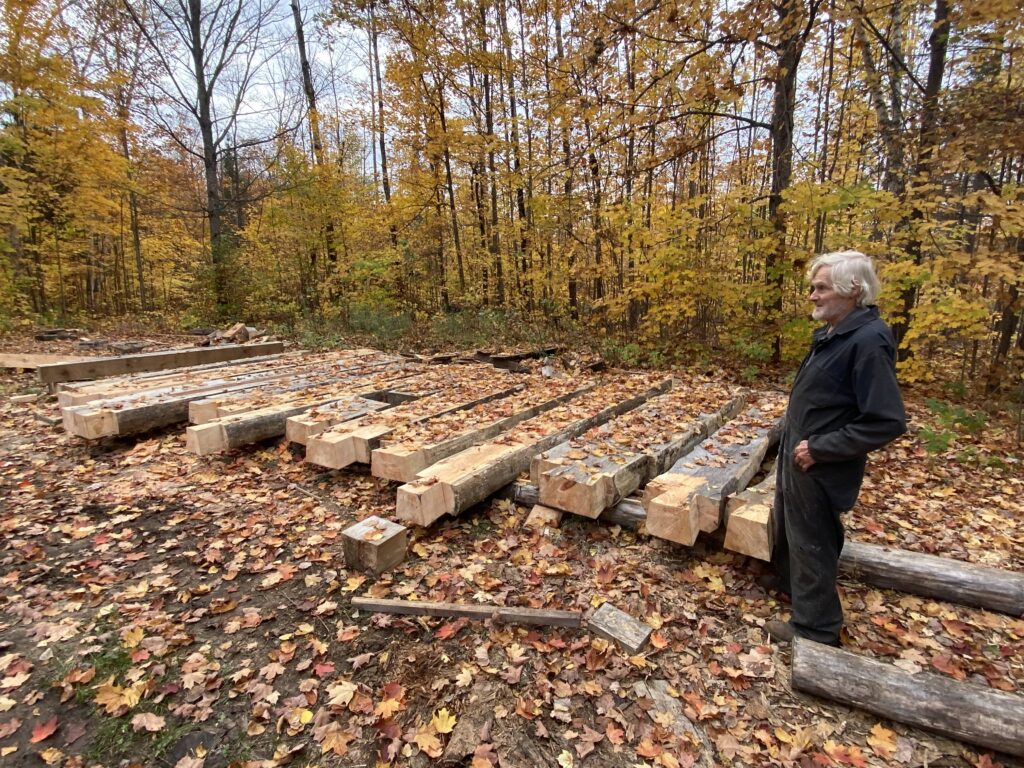
By Nate Smelle
Throughout the mid to late 1800s, logging in eastern Canada transitioned away from the “square timber” era to what has become known as the “saw log” era. In order to speed up production and keep up with technological advances enabling loggers to cut more trees down faster, it has become common practice to transport round logs from the forest to a sawmill. Prior to this onslaught of modern logging practices, loggers felled and cut massive white and red pines into square timbers in the forest, using nothing but a few types of axes.
Although the modern forestry industry has shifted away from the more careful, hands-on techniques used during the square timber era, for nearly three decades Bancroft's John Foreman has continued to employ these traditional forestry skills. Foreman picked up the trade, working alongside local woodsman Henry Taylor on a project in 1992. At that time, he said Taylor – 89-years-old at the time – taught him the art of wielding a broad-axe to make hand-hewn timbers, while reworking the timbers from an old barn into what would eventually become Foreman's home on Maxwell Settlement Road.
Since then, Foreman has been practicing and perfecting his skills with the broad-axe; harvesting trees growing on the property to produce hand-hewn timbers and for firewood. During his career, the 82-year-old woodworker has left his mark on the local landscape through his work on landmarks such as: the Band Shell in Bancroft's Millennium Park; the Logging Museum in Algonquin Park; and, the Ohara Mill. In his spare time, he has also enjoyed sharing his expertise in hand-hewing timbers with people through hosting public educational demonstrations and workshops.
What Foreman said he enjoys most about his craft is the sense of accomplishment he feels after completing a project. Spending so much time outdoors in the forest, he has also developed a deep appreciation of nature. In practicing this rare trade from the forestry industry's square timber era, Foreman is able to produce his unique timber products in a more sustainable manner than large-scale logging operations. For example, by taking extra time to assess which specific trees are the best to harvest; as well as, how, when, and in what order they should be harvested, he is able to minimize the overall impact of cutting down trees on the forest ecosystem.
Pointing to the predominantly maple forest surrounding the clearing where he had laid out the timbers for a 13-foot x 10-foot cabin he recently completed, Foreman acknowledged how the area had previously been logged to allow more desirable species to grow. Acknowledging how he has been clearing this space of poplar trees for many years now to make way for a maple forest, he said he understands that it will be future generations who reap the fruits of his labour.
When the time comes, Foreman said he hopes to be able to leave the place behind to someone who has the same mindset as he does. Providing insight into his mindset, he explained that he has a few rules to guide him. According to Foreman, no matter a tree's size, he will not cut it down unless it is dead, dying, or crowding out another healthy tree. Ultimately, he said his approach to forest management is similar to how one might care for a garden.
“Size has nothing to do with whether I decide to cut,” explained Foreman. “It's the same principle as looking after a garden. Trees are big plants that need room to grow. The bigger the trees are, the more space you need to give them.”
Foreman describes walking into a forested area to scout out trees that are suitable for harvest as being similar to “playing a game of checkers.” Before deciding on a harvest plan, he said he will carefully inspect the site, so that he can fall the trees in an order which creates the least damage to the forest.
“You can calculate,” Foreman said, highlighting the sustainability advantage held by many smaller scale logging operations in Canada. “But you see, high production loggers don't have time to do that calculating, because when the guy comes in with the skidder for the next hitch, he has to have a hitch ready for him, so he has no time.”
By doing these calculations, Foreman said he is able to harvest the trees in a better, less disruptive way using a skidder, than someone using horses who does not take time to consider these factors. Though Foreman prefers to work with white pine, he said it is possible to make a hand-hewn timber out of any type of tree. As long as it hasn't been decomposing on the ground for too long, he said he can even work with fallen trees in the forest.
“I can work with any type of tree, but I like white pine the best,” said Foreman. “Ash and oak, if they are green, they're not that hard to do, but when they dry they're really hard. I don't like doing spruce, because the knots in them get so hard when they're dry. When they're fresh, they're alright though.”
Acknowledging how the COVID-19 pandemic has perked people's interests in traditional “old world” skills and trades such as his, Foreman said he is hopeful that more people will use the opportunity to re-invent their lifestyle.
“I think it's going to really change things,” said Foreman. “There are going to be more people working from home, and going to the office 50 per cent of the time. Then, 50 per cent of the time they don't have to drive. I hope that's what will happen. It will cut down all the traffic and the pollution, and all of that. I am hopeful that will be a good thing to come out of the whole COVID thing.”
Those interested in learning more about the art of hand-hewing timbers, or how to purchase Foreman's forest products can contact: 613-332-3689.
|